3
2025
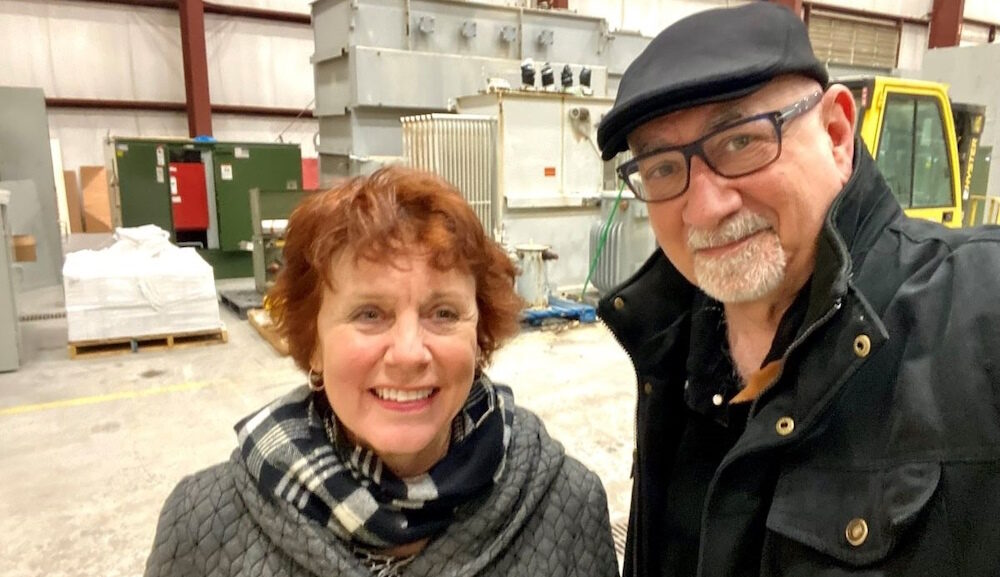
Tracey Nutter (left) of Sunbelt Solomon and Tom Delamater of Pecchia Communications were among those who teamed up on the work instructions.
Sunbelt Solomon, the North American leader in remanufacturing and reconditioning electrical transformers, recently completed comprehensive updates to the standardized work instructions its employees use across the United States.
Revised with support from Pecchia Communications, the instructions now guide the receiving, teardown and assembly of used transformers at the company’s eight U.S. service centers.
“The goal was to give our technicians a clear, consistent understanding of what’s needed and then have the opportunity to refer back and verify they performed the required tasks according to our standard,” said John Gann, vice president of operations East for Sunbelt Solomon.
Before the instructions were revised, many procedures tended to vary by location and even among employees at the same site, who often added changes that were not documented well or shared with other sites.
The task was to establish consistent processes that would be followed at all locations — what Gann called “the Sunbelt Solomon way.”
Pecchia Communications worked with project leaders in Colorado, Kansas, Pennsylvania, Tennessee and Texas to complete six different documents, which provided technicians with step-by-step instructions about how to inspect, repair and recondition large transformers that serve residential areas and industrial sites.
One of the documents was completed just in time for the opening of Sunbelt Solomon’s service center in Elba, Ala. It listed all tools, supplies and personal protective equipment needed before detailing — in 18 pages of words and images — the steps involved in the reconditioning of pole-mount transformers.
“Our lead technician in Elba was new to Sunbelt Solomon and called it the best document of its kind he’d ever seen,” said Gann.
Tom Delamater and Dan Pecchia of Pecchia Communications worked on the project.
“Effective work instructions require professionals who can ask good questions, listen carefully, write with precision and manage the approval process efficiently,” Delamater said.
“Some manufacturers spend enormous sums on work instructions with specialized consultants who don’t communicate well and thus don’t deliver effective documents. Other companies recoil at the prohibitive cost figures they get from pricey consultants and make business decisions to stick with their outdated instructions.
“These very important business tools can be both effective and cost-effective for companies who engage partners with the right capabilities.”
Delamater offered several reasons a company should consider standardizing and publishing its manufacturing procedures, whether they’re performed under one roof or at multiple locations:
Consistency and uniformity of operations. Standardization reduces the risk of deviation from established best practices and maintains quality across different shifts and locations.
Efficiency and productivity. Written instructions clearly outline procedures and reduce the time spent on guesswork, searching for information or asking for help.
Training and development. Instructional documents are essential for training new employees and helping them learn on the job, often with less direct supervision.
Continuous learning. Existing employees can refine their skills or familiarize themselves with updated procedures when updated work instructions are available. This is essential in industries where technological advancements and regulatory changes can influence best practices.
Compliance and safety. Updated instructions help ensure compliance with industry regulations, standards and safety protocols while reducing the likelihood of workplace accidents.
Customer confidence. Adhering to well-documented, consistent processes demonstrates professionalism and assures customers that the work being performed is done according to industry standards.
Latest Posts
- 3 Media Relations Guidelines for an Era of Growing Distrust May 5, 2025
- Brighten Up Your Brand: 3 Tips for a Summer Messaging Makeover May 5, 2025
- Pecchia Comm Lands 18th Major Change Engagement May 5, 2025
- Student Journalism Awards Lead Press Club’s Plans for 2025 March 6, 2025
- Pecchia Comm Plans $20K Grant to Celebrate 20th Anniversary February 26, 2025
- Power of Print Still Endures in Employee Comms February 5, 2025
- 6 Essential Communications Strategies for Managing Organizational Change February 4, 2025
- Factory Work Instructions Drive Compliance, Consistency February 3, 2025
6725 Pheasant Run Drive | Youngstown, Ohio 44406 | Privacy Policy